Glass manufacturing is an intricate and fascinating process that transforms natural raw materials into the elegant, durable, and versatile containers we use every day, such as theGlass Bottlesoffered by Paupacking. To fully appreciate the craftsmanship and technology behind these products, it is essential to understand each step involved in making glass. This detailed guide expands on the entire process, explaining how raw materials become finished glass bottles, highlighting the precision, quality control, and sustainability efforts that Paupacking integrates into every product.
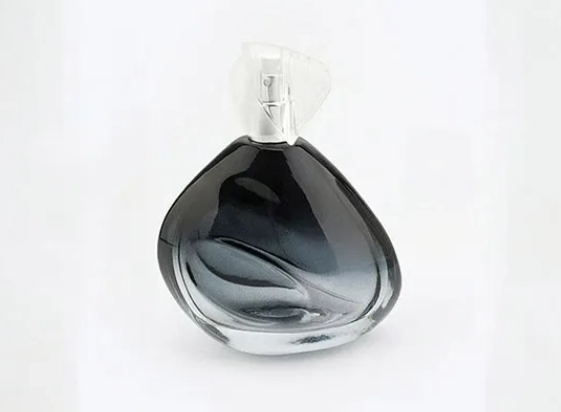
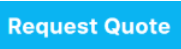
1. Collecting and Preparing Raw Materials
The foundation of glass production lies in the careful selection and preparation of raw materials. The primary ingredients include:
-
Silica sand (SiO₂):The main structural component of glass, silica sand must be of high purity, typically over 99%, to produce clear and strong glass. The sand is sourced from natural deposits and undergoes screening to remove impurities.
-
Soda ash (Na₂CO₃):This acts as a flux, lowering the melting temperature of silica from about 1700°C to roughly 1500°C, making the process more energy-efficient.
-
Limestone (CaCO₃):Added to improve the chemical durability and mechanical strength of the glass.
-
Cullet:Recycled glass fragments are added to the batch to reduce raw material usage and lower melting energy requirements. Incorporating cullet is a critical sustainable practice that Paupacking embraces, helping to reduce carbon emissions and conserve natural resources.
-
Other additives:Depending on the desired properties, metal oxides or coloring agents may be added to produce tinted or specialty glass.
Preparationinvolves weighing and mixing these components in precise proportions to form a homogeneous batch, ensuring consistency in the final product. This step is crucial because any variation can affect the glass’s clarity, strength, or color.
At Paupacking, our commitment to sustainability is reflected in the high percentage of cullet used in ourGlass Bottles, reducing environmental impact without compromising quality.
2. Melting and Refining the Batch
Once the raw materials are prepared, the batch is fed into a furnace where it is heated to approximately1,500°C (2,732°F). This extreme temperature melts the raw materials into molten glass.
This stage includes several critical sub-processes:
-
Melting:The batch liquefies into a viscous, molten state. This transformation requires maintaining a consistent temperature and thorough mixing to ensure homogeneity.
-
Refining:During melting, gases trapped in the batch form bubbles. Refining involves holding the molten glass at high temperature to allow these bubbles to rise and escape, resulting in bubble-free, clear glass.
-
Homogenizing:Continuous stirring or bubbling of inert gases ensures uniform chemical composition and temperature throughout the molten glass.
This melting and refining process can take several hours, sometimes up to 50 hours, depending on the furnace design and glass type.
Paupacking’sGlass Bottlesbenefit from this meticulous process, resulting in glass that is not only visually flawless but also mechanically robust.
3. Forming and Moulding the Glass
After refining, the molten glass is ready to be shaped into bottles or jars. The forming process is highly technical and varies depending on the bottle design and production scale.
Common forming techniques include:
-
Blow and Blow:Primarily used for narrow-neck bottles, this method involves dropping a gob of molten glass into a blank mold. Air is blown into the gob to create a preliminary shape called a parison. The parison is then transferred to a final mold where it is blown again to its final shape. This technique allows for precise control of bottle thickness and shape.
-
Press and Blow:Used mainly for jars and wide-mouth containers, a plunger presses the molten glass into the blank mold to form the parison, which is then blown into the final mold. This method provides better control over the base thickness and is more efficient for certain shapes.
-
Manual shaping:In artisanal or small-batch production, glass may be hand-blown or pressed, allowing for unique designs and craftsmanship.
Modern factories use highly automated forming machines to ensure consistency, speed, and precision. The forming process must balance speed with quality to avoid defects such as uneven thickness or surface imperfections.
Paupacking’sGlass Bottlesare produced using state-of-the-art forming techniques, ensuring every bottle meets exacting standards for shape, thickness, and finish.
4. Annealing: Controlled Cooling to Eliminate Stress
Immediately after forming, glass containers are extremely hot and fragile. Rapid cooling would cause internal stresses leading to cracks or breakage. To prevent this, the bottles undergoannealing, a slow, controlled cooling process.
Annealing involves:
-
Passing the bottles through an annealing oven or lehr, where the temperature is gradually reduced from around 600°C to room temperature over several hours.
-
This controlled cooling relieves internal stresses caused by uneven temperature gradients during forming.
-
The process significantly increases the mechanical strength and durability of the glass.
Proper annealing is essential for the safety and longevity of glass bottles. Improperly annealed glass can fail unexpectedly under thermal or mechanical stress.
Paupacking ensures allGlass Bottlesundergo precise annealing cycles tailored to their specific design and glass composition, guaranteeing toughness and reliability.
5. Inspection and Quality Control
Quality control is a critical phase that ensures only flawless glass bottles reach customers. The inspection process is multifaceted:
-
Visual inspection:Automated optical systems and human inspectors check for surface defects such as bubbles, stones, cracks, or discoloration.
-
Dimensional checks:Bottles are measured for exact height, neck diameter, and wall thickness to ensure compatibility with closures and filling equipment.
-
Strength testing:Samples undergo mechanical tests to verify resistance to impact, pressure, and thermal shock.
-
Leak testing:Ensures bottles and their closures provide airtight seals, essential for preserving contents.
Defective or substandard bottles are recycled back into the cullet supply, supporting Paupacking’s sustainability goals.
This rigorous quality assurance process ensures that every PaupackingGlass Bottlemeets industry-leading standards for performance and safety.
6. Finishing Processes
After inspection, bottles may undergo additional finishing processes to enhance appearance, durability, or functionality.
Common finishing steps include:
-
Polishing:Edges and surfaces are smoothed to remove sharpness or roughness, improving safety and aesthetics.
-
Coating:Protective coatings may be applied to increase scratch resistance or provide UV protection, preserving contents sensitive to light.
-
Coloring:Metal oxides can be added during melting or applied as surface treatments to produce colored glass (e.g., amber, green), which can protect contents and create brand differentiation.
-
Labeling and printing:Branding elements such as logos, instructions, or decorative designs are applied using screen printing, decals, or embossing.
Paupacking offers a wide range of customization options on ourGlass Bottles, enabling brands to create packaging that is both functional and visually striking.
7. Packaging and Shipping
The final step in the manufacturing process is careful packaging and shipping:
-
Bottles are palletized with protective materials such as foam or cardboard separators to prevent damage during transport.
-
Packaging is designed to maintain cleanliness and prevent contamination.
-
Logistics planning ensures timely delivery while minimizing environmental impact.
Paupacking’s meticulous packaging and reliable shipping ensure that everyGlass Bottlearrives at its destination intact and ready for use.
Summary Table: Step-by-Step Glass Manufacturing Process
Step | Description | Purpose/Outcome | Paupacking’s Advantage |
---|---|---|---|
Raw Materials Collection | Silica, soda ash, limestone, cullet | Base ingredients for glass batch | Use of recycled cullet for sustainability |
Melting & Refining | High-temp furnace melts batch into molten glass | Homogeneous, bubble-free molten glass | Produces clear, strong glass |
Forming & Moulding | Automated blow and press methods shape bottles | Precise, uniform container shapes | Consistent, elegantGlass Bottles |
Annealing | Controlled cooling to relieve stress | Durable, crack-resistant glass | Ensures mechanical strength |
Inspection & Quality Control | Visual and mechanical testing | Defect-free, high-quality glass | Strict standards guarantee product excellence |
Finishing | Polishing, coating, coloring, labeling | Enhanced aesthetics and protection | Customizable designs for branding |
Packaging & Shipping | Palletizing and protective packing | Safe delivery to customers | Secure handling preserves product integrity |
Why Choose Paupacking’s Glass Bottles?
Paupacking’sGlass Bottlesrepresent the pinnacle of modern glass manufacturing, combining:
-
Sustainability:Incorporating recycled glass and eco-friendly practices.
-
Durability:Annealed for strength and resistance.
-
Elegance:Crystal-clear, smooth finishes with customizable options.
-
Versatility:Suitable for food, beverages, cosmetics, and more.
-
Reliability:Rigorous quality control ensures consistent excellence.
By choosing Paupacking, you invest in glass bottles that not only meet but exceed industry standards, supporting your brand’s commitment to quality and sustainability.
Conclusion
The process of making glass is a remarkable blend of natural materials, high-temperature chemistry, precision engineering, and quality craftsmanship. From raw sand to the elegantGlass Bottlesthat grace shelves worldwide, every step is carefully controlled to produce containers that are beautiful, durable, and eco-friendly.
Paupacking’s dedication to excellence in glass manufacturing ensures that each bottle delivers superior performance and aesthetic appeal. Whether for packaging food, cosmetics, or specialty products, our glass bottles stand as a testament to the art and science of glassmaking.
Explore Paupacking’s full range ofGlass Bottlestoday and discover how expertly crafted glass can elevate your product offering.